Replacing Crusher Components – What You Should Consider
Many plants have to evaluate whether to do
major component replacements in-house or take advantage of OEM service teams to
complement their site personnel’s efforts. Baden Parker, Senior Manager, Global
Field Services with Metso Outotec, shares his thoughts on what needs to be
considered when dealing with these major service events.
When it comes to replacing major components
for gyratory, cone and jaw crushers, finding the right personnel who are
trained for these specialised tasks can be a challenge. Bottom shells,
mainshafts or gears eventually need replacement or even an upgrade to take
advantage of product improvements. Large and heavy parts often require
specialised handling and installation procedures, as well as specialised tools
to ensure safety.
When replacing an eccentric, a pitman, a
pinion or any other major crusher component, many questions can come up. Has
the site planned this type of work before, and does it have all the right
tools? Are all the service steps perfectly understood to do the work safely and
efficiently? Are there experienced personnel available to execute the part
change-out? Does the site service team know what to look for to make sure the
parts come together properly? Are new parts to be used or are the existing
parts that are going to be re-used in good condition?
Using in-house expertise, OEM support or
both
Many mine sites and plants try to tackle
these types of crusher component change-outs with their in-house capabilities.
However, even with sites that have strong maintenance teams, there are many
challenges that may not be considered. Some sites may have to deal with high
turnover in key service positions, leading to uncertainty in how to perform
these major and non-routine maintenance tasks. Other plants need to service
many models and brands of equipment and may not have the specialised knowledge
that comes from performing complicated parts’ change-outs on a regular basis.
There is also the constant struggle between production and maintenance aims and
goals. When the pressure is on to increase production, there can be the
temptation to shortcut maintenance times, which can lead to equipment problems
or safety concerns that outweigh the time saved doing the actual work.
Having served at mine sites for 10 years, holding roles such as Shift Mechanical Fitter, Leading Hand, Supervisor, Senior Supervisor & Maintenance Planner before joining Metso Outotec as a crusher maintenance expert, has given me a broad view when it comes to service operations. I gained considerable knowledge on the life cycle of a site’s crushing assets and the maintenance required to ensure equipment reliability and, in turn, plant availability. I can say with confidence that if the on-site crews are well trained, many routine tasks can be handled safely and competently. However, a typical maintenance mentality that I observed (and personally held for some time) is ‘We can fix anything ourselves’ and that calling in the OEM was not needed, as we could work out the best ways of working ourselves. For many routine component replacements, this was indeed true enough.
Combining approaches for highest crusher uptime
Having strong in-house site teams
to service crushing and screening equipment can bring many benefits and cost
savings to a plant. However, complementing their efforts by having an OEM
service team either execute or supervise larger, more complicated, or less
often performed component replacements should always be considered and can
bring the best of both worlds. Leveraging OEM know-how for major component
replacement can pay dividends in terms of smoother change-outs and higher
equipment availability due to less issues and rework caused by small missteps.
By utilising Metso Outotec
crusher component replacement services, sites can benefit from the OEM team’s
experience in scheduling and staging pre-outage activities, as well as
executing the work quickly to significantly reduce downtime. It also brings the
advantage of having one point of responsibility for the entire maintenance
event. In some cases, OEM warranties can often be extended when Metso Outotec
crews perform the installation of major parts. With access to global knowledge
centres, trouble shooting and adjustments can often be done on the spot by our on-site
crews, bringing further uptime benefits.
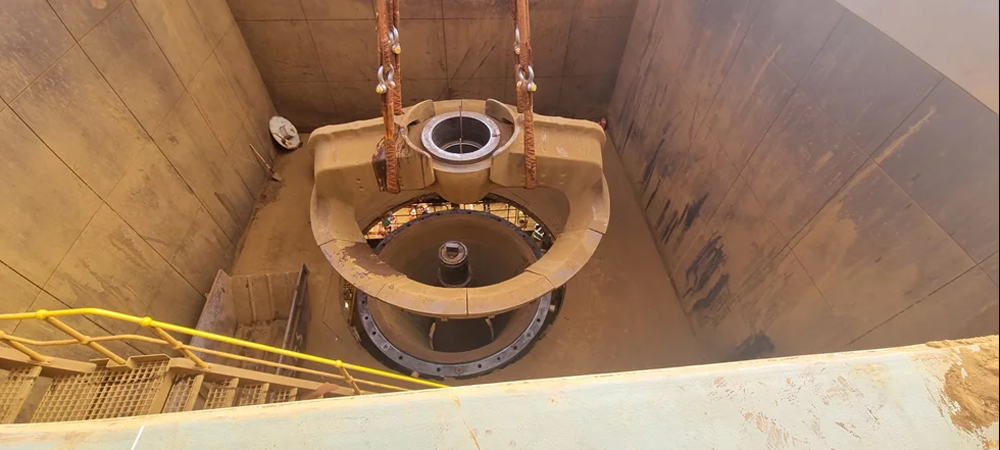




